产品检验程序
1.0目的
为有效控制来料产品、制程产品、成品品质,降低不良,特制订本程序。
2.0范围
本公司来料产品、制程产品、成品之检验作业。
3.0权责
本程序由品管制定及维护,相关单位配合执行。
4.0定义
4.1严重缺点:指产品根本不能使用或影响人身心安全的缺点。
4.2轻微缺点:指产品不影响正常功能的缺点(例:外观不良)。
4.3免检物料:指对产品质量影响小、产品品质一贯稳定或现有条件难以检验其性能而采用免检控制方式的物料,其控制方法为验证、试用。
4.4首件检验:指对制程第一件或操作条件变更、制品规格变换批量生产之前首件制品给予检验。
4.5自检:操作人员对自己生产的产品按品质要求进行检查。
4.6巡检:在生产过程中对各生产工序之半产品进行巡回检查。
5.0内容
5.1进料检验:
A.供应商交货时,仓管员依厂商送货单及工厂采购单先办理确认点收手续,然后将物料放置在“待检区”内,再通知品管检验。
B.检验员收到通知后,确认是否为“免检物料”,若属之,则由仓库填写《入库单》进行入库。反之,则由品管按进料检验标准抽取样本,并准备适当的检验工具,实施检验。
C.检验完毕品管填写《进料检验报告》并作品质判定,并于实物上标明检验结果,仓库依此开出《入库单》进行入库。
D.进料检验结果由品管汇总,作为对供应商考核的依据。
5.2制程检验:
A.作业员按照生产任务要求予以生产,检验员及作业员依据相关检验标准对制程品予以检验。
a.首检:每工序/每工段产品均须进行首检,由检验员填写《首检报告》并确认合格后方可正常生产。
b.自检:生产过程中各员工应对生产的产品进行自检。
B.制程品管依据相关检验标准,随机对制程品予以巡检,检验完毕依据检验结果填写《制程检验报告》并作品质判定。
C.首检、自检中发现不合格时,应立即停止生产予以处理,制程品管巡检时发现制程不合格时,应立即反馈生产车间予以处理。
5.3成品检验:
A.生产单位加工完毕,通知品管检验。
B.品管依据成品检验标准实施最终检验,检验完毕依据检验结果填写《成品检验报告》交由品管主管确认后并作品质判定。
C.超过保存期或异常的成品复检:仓库于盘点时,发现有超过保存期的或异常成品时,应及时知会品管依据《成品检验标准》实施复检,检验完毕,须填写《成品检验报告》。
D.若客户有退货时,由品管依本程序对退货品实施最终检验。
5.4检验完毕,品管/作业人员对检验结果并依据《产品标识和可追溯性程序》进行标识。
5.5检验时发现的不合格品依据《不合格品管理程序》处理。
5.6制程检验/成品检验过程发现严重品质异常,依据《质量改进程序》处理。
6.0附件
6.1进料检验报告
6.2自主检验报告
6.3制程检验报告
6.4成品检验报告
7.0参考文件
7.1产品标识和可追溯性程序
7.2不合格品管理程序
7.3质量改进程序
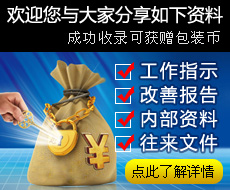