柔版印刷常见故障及解决办法
柔版印刷常见故障及解决方案
一、印版空白部分粗化表面磨损后易出现故障
印版经过长时间的印刷,空白部分的粗化表面可能会逐渐被磨平,导致:
(1)印版的涧湿性能降低,必须增加润版液的供应量,才能维持水墨平衡。
(2)印版表面储存的水分减少,吸附在印版表面的胶体变少,如果印刷中途短暂停机,不及时擦胶就很容易起脏,给生产带来极大的不便。粗化表面磨损比较严重的话.就必须更换印版。
二、水墨印刷常见故障及解决方法
1、承印物粘结、蹭脏
故障原因:1.水墨不干;2.复卷张力太大;3.存放印刷品的室温太高
排除办法:1.提高干燥温度;3.降低复卷张力;4.印刷成品放在凉爽处
2、糊版、堵版
故障原因:1.印版太浅;2.印刷压力太大;3.供墨量太多;4.水墨粘度太高;5.水墨干燥速度过快;
排除办法:1.加深印版;2.调整印刷压力;3.降低供墨量;4.降低水墨的粘度;5.降低干燥温度
3、叠色不良
故障原因:1.多色套印中印后面的颜色时,前一色未干;2.后印的颜色使前一色发生剥离现象;3.后印的色叠印不上去
排除办法:1.提高第一色干燥速度;2.降低后印色墨的粘度或降低印刷压力;3.降低后一色的粘度或提高其附着力
4、印刷针孔
故障原因:1.水墨在墨辊上干得太快,传墨不匀;
排除办法:1.减慢水墨的干燥速度;
5、颜色太浅
故障原因:1.水墨的粘度太低;2.网纹辊网线太细;3网纹辊磨损或未清洗干净;4.上墨量太小
排除办法:1.提高水墨的粘度;2.调换粗网线的网纹辊;3.换用新的网纹辊或对网纹辊进行彻底清洗;4.降低传墨辊或刮墨刀的压力或适当增加版滚筒压力(凹版),加快印刷速度(柔版)。
6、颜色太深
故障原因:1.水墨的粘度太高;2.网纹辊太粗;3.水墨色饱和度太高;4.上墨量太大
排除办法:1.加稀释剂降低粘度;2.换细网纹辊;3.加撤淡剂降低颜色深度4.提高传墨辊或刮墨刀的压力或适当降低版滚筒压力(凹版)
7、印刷品有斑点
故障原因:1.塑料薄膜厚薄不均匀;2.水墨太稀薄;3.水墨的粘性大;4.印版涂墨不匀
排除办法:1.调换厚薄均匀的薄膜;
2.加新配的水墨;3.增加水墨的粘性;4.从水墨和供墨检查传墨不匀的原因
8、墨色不匀
故障原因:1.印版不平整;2.承印物厚度不均匀;3.传墨不匀,如网纹辊磨损;4.网纹辊网线数太低
排除办法:1.印版背后研磨,或贴胶纸校正;2.调换厚薄均匀的的承印物;3.更换网纹辊
9、线条边缘发毛
故障原因:1.水墨干燥速度太快;2.压力不匀,压力调节不当;3.环境灰尘的影响
排除办法:1.降低水墨的干燥速度;2.调整印版与网纹辊之间的压力;3.减少环境灰尘
10、套印不准
故障原因:1.收、放料张力不均匀;2.薄膜有荷叶边;3.薄膜接头不平;4.前一色压力太大,使图象变形
排除办法:1.调节收、放料张力;2.调整张力、更换薄膜;3.重新接头;4.调节印刷压力
11、印刷牢度差
故障原因:1.塑料薄膜电晕处理不足;2..塑料薄膜印刷适性极差;3.墨的粘附力不够
排除办法:1.塑料薄膜重新处理,要求表面张力处理到40达因以上;2.更换塑料薄膜;3.向本公司提出改进要求
12、颜色不稳定
故障原因:1.粘度或PH值有变化;2.操作过程有误;3.配墨过程有误
排除办法:1.检查粘度和PH值与上次印刷时有所变化;2.检查操作程序3.向本公司反应质量事故
13、起泡
故障原因:1.印刷速度太快;2.加入过多稀释剂或硬度高的自来水
排除办法:1.2.加入消泡剂
14、干燥速度太快
故障原因:1.印刷速度太慢;2.敞开放置时间过久;3.墨干燥速度过快;4.干燥温度太高
排除办法:1.提高印刷速度;2.添加稀释剂;3.加入慢干剂调节;4.降低干燥温度,甚至不需要干燥系统
15、干燥速度太慢
故障原因:1.印刷速度太快;2.墨干燥速度太慢;3.干燥温度低
排除办法:1.降低印刷速度;2.添加慢干剂; 3.提高干燥温度
三、印版耐印力低的原因及其处理方法
原因:
1.水辊对印版的作用力太大;
2.印刷时印版与橡皮布间的作用力太大;
3.堆版后没及时擦洗橡皮布;
4.印刷纸张中纸粉太多;
5.纸张PH值过高或过低;
6.润版液PH值不当;
7.版基金属成分不合乎印版要求;
8.印刷纸张中有沙土或砂粒;
9.印版本经阳极氧化,表面没有形成坚固、致密的三氧化二铝腊层;
10.橡皮装倒;
11.印版保存不当受到了强光照射,有微量曝光现象;
12.制版时显影过度;
13.橡皮布老化;
14.油墨粘度太高;
15.晒版时所用软片密度不够;
16.印版存放时间太长,其感光树脂膜发生了质变;
17.修版后擦拭余存的修版膏(剂)时用水量太小且没有向非图文处擦试,致使印版树脂膜有减薄现象;
18.水辊套过于老化;
19.靠版墨辊对印版的作用力量太大且印刷速度快,致使印版咬口部位易损坏;
20.印版感光树脂膜厚薄不一;
21.印版砂目太粗;
22.在印版没上墨情况下,水辊作用在印版上,机器空转太久;
23.用润湿粉剂擦版时间太长且用力过大;
24.靠版水辊挂墨太多并且油墨在水辊上硬化所致;
25.上版时印版背面料有脏物,致使上版后印版部分部位凸起过高的;
26.纸张易掉粉且印刷时用液量太小,易时常堆版所致;
27.橡皮布两侧和脱尾积存的墨垢太多;
28.印刷机滚筒轴套磨损严重,印刷时对印版的碰击力量增大所致;
29.橡皮布衬垫硬度太高,容易磨损印版;
30.烤版过度;
31.印版树脂膜质量太差,且版面砂目过于尖锐;
32.靠版墨辊老化,印刷时碰撞印版严重所致;
33.橡皮布固定太松;
34.所使用的油墨老化太严重;
35.橡皮布应该清洗时未清洗并连续使用;
36.橡皮布衬垫或衬纸不平;
37.印刷时用墨量太小,且印刷速度快;
38.印版与橡皮间作用力量太大或者橡皮与压印间的作用力太大,致使橡皮布易于伸缩,从而易磨损印版;
39.纸张轻微打皱处易积存纸粉;
40.印版与橡皮间两端压力差距大或橡皮与压印间的两端压力差距大;
41.印版衬垫上粘有脏物,印版部分部位凸起过高所致;
42.橡皮衬垫上粘有脏物,橡皮安装后部分部位凸起过高导致;
43.橡皮布两端紧度不一,一端太紧,一端太松;
44.擦版纱布过于老化,擦版时损伤了印版树脂膜所致;
45.印刷机滚筒轴向窜动严重;
46.印版衬垫不厚或橡皮衬垫太厚。
处理方法:
1.用塞尺作相应调节、调节时可把印版反过来,以免损伤印版砂目,同时印版总衬垫应符合要求,调节后水辊对印版作用力一般在0.2-0.5mm范围内,但也要根据具体情况来确定,如“新水辊套在调节时应与印版作用力稍小些,随着使用程度不同再逐渐调节;旧水辊对印版的作用力应适中。因旧水辊套变化性较小,作用力较大也较易于摩擦印版;
2.用千分尺进行具体调节,一般情况下压力在010-0.15mm范围内,还应注意印版厚度的不同对印刷压力的影响;
3.应根据纸张情况、油墨流动度大小、图文情况和印量大小来及时擦洗橡皮布;
4.尽量少使用纸粉较多的纸张,即使使用也宜常擦洗橡皮布和不断添加新油墨等;
5.最好避免使用,即使使用也应在低印量的印品上,印刷时水斗液PH值宜保持在5-6之间;
6.水斗液应呈弱酸性,并且水斗宜常作清洗,以免水斗液腐化变质;
7.更换印版,即使使用也应在质量要求不高且印数较少的印品中,印刷过程中应注意印版使用程度,以免影响产品质量;
8.不应作印刷用;
9.选用在低印量且印品质量要求不高的活件中;
10.改换橡皮布使用方向。为了避免安装时有误,最好的办法是用手抓住橡皮市两端拉一拉,伸长不明显的为使用方向,也可以用鉴别橡皮布背面标示的办法来判定其使用方向;
11.更换印版或在低印量的印品中使用;
12.制版时应根据显影液情况和印版感光度大小来正确显影,因显影不当致使树脂膜减薄的应更换印版;
13.更换橡皮布;
14.用调墨油、撤粘剂、改良剂等作适当调整,并且要根据印品情况和油墨类别来确定用量;
15.因晒版软片密度不够致使的印版质量问题,应杜绝使用;
16.最好避免使用,即使使用也应在低印量且印品质量要求不高的活件中;
17.修版后擦试修版膏(剂)时,应一边用大水量冲洗一边向非图文处擦试;
18.更换水辊套;
19.用塞尺调节好墨辊,同时应注意印版衬垫总厚度是否符合要求;
20.更换印版;
21.宜在质量要求不高且印数较少的印品中使用;
22.在印版不上墨的情况下,水辊作用在印版上机器不宜空转太久;
23.用润湿粉剂擦试印版上的脏污时,对图文部分不得用力太大,以免损伤印版树脂膜;
24.应用清洗剂或汽油洗刷水辊,洗刷后水辊套上不得余存清洗剂或汽油残存液,应反复刮除净;
25.上版时应注意检查背面,因不注意检查致使上版后印版部分部位有凸起现象的,应拆卸下印版并放在平整的物体表面上,从印版正面凸起处的上方压快厚些的片基用较平滑的木板或竹板挫平,操作时应注意不要使片基滑动,也不宜用力过猛,以免损伤砂目;
26.纸张易掉粉的、印品质量要求不高的且不作套印的印品,可稍加大些润版液用量,以使油墨有良好的转移性,同时也应注意选用抗水性较强些且不易乳化的油墨;
27.橡皮两侧和尾部易带脏,宜常擦洗橡皮和压印滚筒相对应的部位;
28.更换相应配件或进行妥善修复,不更换配件的应注意减速印刷;
29.较正常硬性衬垫硬度太大的不应使用,以免机器产生较大的振动或容易使印版受到严重的磨损;
30.烤版后如果版面呈现黑棕色或更为严重的灰黑色,一般不同;
31.更换印版或在低印量的活件中使用;
32.靠版墨辊老化严重的应更换,不太严重的可用橡皮清洗还原剂清洗,印刷时车速也不宜太快;
33.橡皮布固定太松的应给予紧固,尤其新更换的橡皮和衬垫使用一段时间后易出现松弛现象,应注意及时紧固;
34.因油墨使用时间长或因混入较多纸粉的应更换油墨;
35.换版后应注意擦洗橡皮布,不得连续使用;
36.展平或更换橡皮衬布或衬纸,因衬垫不平引起的橡皮布损伤应及时修复或更换;
37.在印刷时,油墨本身对印版树脂膜有一定的保护作用,用墨量太小较容易磨损印版;
38.选定好滚筒中心距,并用千分尺测量好压力,一般情况下,压力在0.10-0.15mm范围内;
39.宜常擦洗橡皮布,当纸张轻微打皱处积存较多的纸粉时,应进行局部清理,以免较容易磨损该处印版;
40.用千分尺调整使其压力平衡;
41.拆卸下印版。衬垫清除所粘附的杂物,印版某些部位凸起的应从正面压张片基用平滑的木板挫平;
42.拆卸下橡皮布衬垫清除障碍物,橡皮布或衬垫有损坏现象的应更换或进行妥善修复;
43.拆下橡皮布,剪去或切去原孔眼,用尺子量好平行尺寸重新打孔;
44.更换擦版纱布;
45.紧固滚筒轴套或更换相应配件;
46.用千分尺测量出所需的厚度。
四、油墨因素引起的脏版、花版、糊版
1、油墨粘度过大而产生花版
油墨粘度过大,除了使印迹转印困难外,还会破坏墨层中间断裂的条件,使版面剩余墨层不足,因图文部分裸露受磨损造成花版。
处理方法:适量加一些去粘剂降低油墨粘度,而并不使油墨流动性增加太多。对于印制精细产品,降低油墨粘度,以采用防粘剂为好,因为它在降低粘度的同时,并不增加油墨的流动性,并且对油墨干燥有好处。可是加用量要适当,用量过多会影响印迹光泽,一般黄墨加用量1%~1.5%,其他色油墨在2%左右。
2、油墨粘度太小易糊版
粘度小的油墨易乳化,造成浮脏,使油墨不能正常地转移,使墨辊,印版和橡皮布上逐渐堆积颜料颗粒。当颜料颗粒在印版上堆积到一定厚度时,就会引起糊版。有时因版面剩余墨层不足造成花版。
处理方法:适当加进一些浓调墨油,但不能加入太多,避免影响其他性能。
3、油墨流动性过大会使网点扩大变形,油墨流动性不足产生花版
油墨流动性过大会使墨层铺展,使印迹几何尺寸扩大,印迹不能正确复制。油墨流动性不足往往油墨分布不匀,造成印版受墨不足而花版。
处理方法:油墨流动性对所有印刷机并不完全适应,高速机比低速机要有较大的流动性。调节油墨流动性的材料一般用6号调墨油和高沸点煤油。但要注意不要把机油或其他不干性矿物油加入油墨中。
4、油墨颗粒粗而产生花版
油墨颗粒粗,在印刷表面起到磨料作用,在千百次滚压中,使图文基础受到破坏而造成花版。
处理方法:印刷时尽可能选用比重小的颜料制成的油墨。对于冲淡色墨一般应采用透明冲淡墨或亮光浆作为冲淡剂,而不要用白墨。
5、油墨中燥油太多而糊版
在印刷中有些操作者为使印件快速干燥,就往已具备干燥性能的油墨中加入干燥剂,促使了墨辊的老化程度,并使油墨变粗,乳化,使印版上的墨层不能从中间断裂,多数留在印版上,造成堆版。在印刷压力作用下,使网点上墨层逐渐扩大造成糊版。
处理方法:对于因燥油太多而引起的糊版,不能用增大版面水分的方法来解决,应当将墨辊上的旧油墨清洗掉换上新墨。在印件需要加入适量燥油的油墨,当停机时间短时,可在墨辊上涂些防干剂,当停机时间长时,就应把墨辊上油墨清洗干净。
五、油墨引起的印刷故障成因及处理方法
油墨是印刷用的着色剂,是印刷的主要原料。油墨对印刷质量的优劣有很大的关系,特别是当油墨性能不适合印刷的时候,会引起工艺上的一系列故障,严重影响生产的正常进行和产品的质量,印刷者必须改变油墨的某些性能以适应印刷的需要,但有些工艺故障不单是由油墨造成的,还与其他因素相关,所以印刷操作者必须认真分析,正确处理。
本文先就油墨在印刷过程中所引起的故障及处理方法进行论述,希望能有所帮助。
1.油墨堆墨
现象及原因:在印刷的过程中,从墨斗下来的油墨不能平衡经过墨辊、印版和橡皮布转移到纸上,而是堆积起来,失去了良好的传递。发生这样的情况,除了机器的压力不合适以及橡皮布过硬等因素外,常见的还有如下原因:
(1)连结料粘度不合适,没有足够的粘合度把颜料传递,而使得部分颜料的颗粒堆积在墨辊、印版及橡皮布上。
(2)颜料颗粒愈粗或比重愈大,连结料对其的传递能力就愈差,愈没有足够的能力将其传递,从而使油墨沉积在墨辊、印版及橡皮布上。这种情况常见于印刷黄墨时。因油墨中黄颜料的比重较大,可占75%,颜料愈重,连结料的连接力就显得愈重要。
油墨印刷时极易出现堆墨现象
(3)油墨中含油量太少,颜料颗粒没有足够的连结料来堆积。
(4)油墨粘度太高或太硬,其流动性就小,印刷墨斗里的油墨不易下到墨辊上,如果油墨间的吸附粘力大于印版、橡皮布及纸张对油墨的吸附力,则油墨仍会堆积在墨辊、印版及橡皮布上。
(5)油墨中燥油加放太多,会使油墨在墨辊上干燥或使油墨变粘,尤其在夏天或停机时间过长时,一旦油墨在墨辊上干燥,它就失去传递性能,墨斗下来的油墨就堆积在墨辊上。
(6)纸张质地疏松或“脱粉”,致使纸毛及粉质混入油墨中,也会产生堆版及堆橡皮布。处理方法:
(1)由于连结料粘性差或颜料颗粒粗、比重大,可加0号调墨油或树脂油来增加粘度提高传递性能。
(2)由于油墨粘度太大、太硬,纸张质地疏松、脱粉、或含油量不足,可加6号调墨油、康邦、凡士林、维利油等来改变油墨粘度,增加润湿性能。
(3)减少燥油量(加新墨)或适当地加些不干性的辅料。
(4)油墨颜料颗粒粗,比重大,增加粘度仍不能解决可将油墨在轧墨机内碾轧后再使用。
(5)如改变某些性质后,还不能彻底解堆墨现象,可与多洗胶辊、印版、橡皮布等方法相结合进行处理。
2.花板
现象及原因:花版是网点逐渐变小而脱落,印版失去良好的感脂能力,使印刷品的层次减少,墨色减淡。造成花版的原因很多,例如滚筒、水辊、墨辊的压力太大,水斗药水太大或水分太大,纸张沙粒太多或橡皮布太硬等,常见的由油墨造成花版有如下原因:
(1)油墨颜料颗粒太粗太硬,对版面的摩擦就大,特别对细小网点处,磨擦破坏了图纹吸墨基础造成了花版。有些颜料,对版面有轻度的腐蚀,破坏版面图纹的吸墨基础,同样也会造成花版。
(2)油墨的油性不足,对酸性药水的抗拒能力弱,版面图纹基础上的墨层被酸性药水侵入而造成花版。
(3)油墨的粘度不合适,粘度过大油墨内聚力也大,在传递过程中,在墨层不易断裂,造成版面图纹基础上的剩余墨层不足而花版;粘度过小,油墨对版面的附着力不强,版面的图纹基础得不到应有的剩余墨层来保护,图纹基础直接受到酸性药水的侵入和磨擦而造成花版。
处理方法:
(1)油墨油性小,粘度低、附着力小,常见于黑墨和915冲淡墨,可适当添加些05——90或05--93亮光浆,以改善性能(黑墨不要超过10%)。
(2)油墨粘度过大,造成版面剩余墨层不足而花版,可加放6号调墨油或康邦等撤粘剂来改善。
(3)油墨颜料颗粒太粗,腐蚀性太强(例铬黄墨),调换油墨或将油墨碾细后再用。
3.糊版
现象及原因:糊版时版面图纹不清,网点线条扩大,相邻网点相互并合,使印刷品墨色很深并发粗,层次减少。糊版的原因除药水太谈、辊筒压力过大以及橡皮布绷得过松等因素外,常见由油墨造成的有如下原因:
(1)油墨调得太稀薄,质地太松,其内聚力较小,极易向外铺展,造成网点及线条的扩大。
(2)下墨量大,超过版面图纹所能容纳的墨量时,向外铺展而造成糊版。
精细网印刷要严格控制油墨质量,否则极易糊板
(3)油墨颜料太粗或粉质太重,连结料对其传递性能降低,造成沉积在版面上阻塞网点。另一方面因颗粒太粗,细网容纳不下而向外扩展,同时对版面磨擦加大,破坏了空白部位的亲水性能使其感脂,致使相邻网点互相并合而糊版。
(4)油墨油重,使版面的空白部分感脂而产生糊版。如果油墨中加入的辅助料太多,能降低油墨的粘度、墨质变松而且使油墨的油性加大,也会造成糊版。
(5)油墨堆积在印版上,阻塞网点的空隙,扩大线条,引起糊版。
处理方法:
(1)油墨发生的糊版常见于金、红墨,可在水斗中适当加些阿拉伯树胶。也可用915维利油和05-93亮光浆各一半冲淡,使用效果较好。多数因油墨调得太稀,造成油墨过于稀薄而产生的糊版,可调换新墨或适当加些浓调墨油。
(2)下墨大时可把油墨颜色调色后,减少下墨量。
(3)减少康邦等辅料用量以控制糊版。
(4)堆版造成的糊版要从堆版的根本原因解决。
4.脱墨
脱墨的原因:脱墨指油墨在墨斗内不随墨斗转动,而与墨斗轴分离,使得串墨辊、匀墨辊不上墨。说墨后,将影响墨辊正常传墨,使印版得不到所需要的油墨而变淡,造成印件墨色深浅不一。常见的脱墨有如下原因:
(1)油墨油性不足,粘度小,不能带动油墨随着墨斗轴的转动而运动,引起脱墨。
(2)油墨流动性差,不易流入墨刀轴与刀片之间,影响下墨引起说墨。
(3)油墨胶化成冻胶状态,使粘度和流动性降低,失去印刷性能,而静止在墨斗上引起脱墨。
(4)油墨含油量太少,粉质太多,不能很好的传递颜料颗粒而停留在墨斗内形成脱墨。
(5)油墨干燥太快,使墨斗轴干结固化,失去传墨性能,并阻塞墨斗辊与刀片之间的间隙,形成脱墨。
(6)油墨内墨皮、残渣等杂质过多,阻塞墨斗与刀片之间的间隙,影响下墨形成脱墨。
(7)水斗药水酸性太强或阿拉伯树胶液用墨过多。
(8)版面水分太大。
处理方法:
(1)油墨问题造成的墨辊脱墨,黑墨较为多见。以油烟里灰制造的油墨油性大,不会产生脱墨。而以炭粉为原料的黑墨油性差,脱墨现象时有产生,可用稀调墨油调稀一些,如果产品图像反差大,不能将墨调稀时,可在墨中滴些油酸解决。
(2)油墨粘度小且墨丝短,常见于用撤淡剂调配的浅色墨,这种油墨极容易乳化,水斗中酸液侵入油墨中,腐蚀墨辊表面,使墨辊表面产生亲水层,从而排油脱墨,这时可适当在油墨中加入浓调墨油,以增加粘度。
(3)发生墨辊脱墨现象后,应尽量减小版面水分并降低水斗药水酸度,去掉阿拉伯树胶液。
(4)油墨太厚太硬,适当加入6号调墨油来增加其流动性。
(5)勤搅动墨斗并去除墨斗内里皮及杂质,防止油墨干燥或胶化,防止脱墨现象。
5.油墨乳化
现象及原因:水分成细小的液滴分散在油墨中称之为乳化,在印刷过程中油和水并不是绝对不相调和,由于油墨和水分的经常接触,且在机械力的作用以及其他因素的参与会存在着不同程度的乳化。在印刷黄墨和淡蓝墨时,这种现象常会出现,而且大都在墨辊两头产生。油墨的乳化对印刷有很大的危害性,冲淡墨色,影响印迹干燥,产生浮脏,油墨发“懈”、墨辊脱墨,印迹变色失去光泽,纸张变黄或变蓝,影响产品质量等不良后果。造成油墨乳化的原因主要是油和水之间的表面张力降低了,除了版面水份过大、水斗药水酸太强、树脂含量太多,纸张表面的活性物质的脱落等因素外,常见油墨乳化的原因有:
(1)油墨的酸值过高,油墨和水的分界面上的表面张力取决于它们的极性差,油墨的极性常以酸值衡量,油墨中游离脂肪酸的含量越多,酸值越高,极性越强,乳化的可能性就越大,一定的酸值能保证油墨中颜料的分散度和转移过程中油墨的附着力,但酸值过高是促使油墨乳化的最大原因.
(2)油墨颜料的抗水性差,特别是胶印用油墨的颜料,既要不溶于水及酸,又要具有抗水的性质,由于普通的色淀颜料的体质料往往是亲水性的粉末,颜料中的染料成分遇到酸性水后,染料会很快析出溶解水中,造成乳化故障。
若油墨颜料的颗粒较粗、粘度不够、轧制过程中同连结料的结合不够牢固,在印刷过程中与酸性接触后极易吸收水分而自身产生膨胀,逐渐与连结料脱离而产生乳化。
(3)印版两端没有图文,水分较大,促使两头产生乳化。
(4)油墨中冲淡剂加放太多,常用的辅料白油的成份是碳酸,维利油的成份是氢氧化铝,本身都是乳化剂,所以辅料加放越多,越会促使油墨乳化。油墨中催干剂加放过多,印刷过程中必然要增加水斗药水的酸性,酸性太强极易引起油墨乳化,加之催干剂本身就是强乳化剂,所以油墨中催干加放越多,越能引起油墨产生乳化故障。
处理方法:彻底解决油墨的乳化是不可能的,因为油和水在机械的作用下,本身就会产生乳化,微量的乳化对印刷的影响不大,如果乳化严重就须加以解决。
(1)调换新墨。
(2)在油墨中加入浓调墨油、减少药水酸度和阿拉伯树胶的用量。
(3)少加油酸、白油及维利油。
(4)减少催干剂用量。
6.拉纸毛
现象及原因:拉纸毛是指油墨和纸张两者之间不能很好的适应,把纸面的纤维拉起,图纹印迹出现白斑点现象。产生拉毛的原因除纸张纤维结构松驰外,由油墨造成的有如下原因:
(1)油墨粘性太强。
(2)油墨流动性太小。
(3)燥油加放太多,使油墨变粘变厚。油墨粘度太大或太厚(燥油太多,而出现的变粘变厚)其内聚力就大,印刷时橡皮布上油墨转移到纸张上的张力也就增大,如果纸张纤维之间的内聚力(结合力)小于油墨间的内聚力,则纸张纤维结构就会被破坏而出现拉纸毛现象。
处理方法:
(1)油墨粘性太强,可加康邦、凡士林,来改变油墨粘度。
(2)油墨太厚、流动性差,可加6号调墨油稀释。
(3)燥油过多或油墨变粘、变厚,可适当加入新墨解决。
(4)如已将油墨调整后,拉纸毛现象仍然严重时,可采用套印一次白油打底的方法来解决。
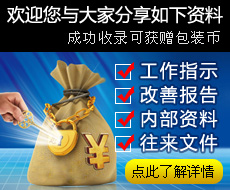