检验程序
检验程序
1. 目的:
规范公司各项检验作业,确保材料及流程中产品符合规定要求,最终产品满足客户要求。
2. 适用范围:
适用于本公司各原、辅助材料、半成品、成品的来料,制作及入库的检验作业。
3. 权责:
3.1仓管员:对来料的一般性确认。并通知IQC验收。
3.2 IQC:按验收标准进行检验。
3.3 PQC:对生产过程的控制及验收。
3.4 FQC:对成品入库的验收。
4. 名词定义:(无)
5. 作业程序:
5.1入检程序:IQC按MIL-105E中的2.5对来料进行抽检。
5.1.1 IQC在验收中如是合格的开具“进料验收单”,一式三份,一份自留;一份交仓库;一份交采购部,并在“进料验收单”上盖合格章后通知仓管入仓,由仓管员在来料中贴上“产品标识单(仓库、品管两种)”
5.1.3 如IQC在按检查标准中查到有不良品,由IQC填写“IQC不合格报告”交品管经理,并在不良品中标上“不良品传票”,以作标识。而对不合格品的处理参照《不合格品控制程序》。
5.2工检程序:
5.2.1 PQC按“PQC日检验标准单”上的要求确定检验的步骤及其控制方法进行检验。在检验时要求各工序首件确认签版及制程中的巡检检查记录,要求巡检时间为15分钟或半小时一次。
5.2.2 在彩印车间印刷过程中,彩印PQC进行首件确认检测,并签版两份,车间PQC各执一份。同时每隔15分钟或半小时作随抽样检测,并填写“制程巡检记录表(彩印)”。
5.2.3 PQC在检验过程中,如实将检查结果填入“制程巡检记录表(纸箱)”中,并通知车间主管对各制作过程进行监控。如小毛病的能解决的则由车间主管自行处理解决。当车间无法自行解决时,按《纠正与预防措施》执行。
5.2.4 PQC在检验过程查出来的较大批不合格品,填写“PQC不合格报告”并按《不合格控制程序》进行。
5.2.5 每天下班前,PQC应填写好各工序的“PQC检验日报表”上报品管文员,由该文员收集整理数据后,交品管经理确认。
5.3最终检查程序:
打包前对产品追踪检查:
5.3.1 FQC在接到最后工序组长通知检验时,按“MIL-105E随机抽检标准”中的2.5执行标准进行检查。
5.3.2 FQC对不合格批盖FQC不合格章,并填写“FQC不合格报告”交品管经理,由品管经理与车间主管查明原因,作出处理并上报生管部和总经理。
5.3.3 所有检验出来的不合格成品,按《不合格品控制程序》进行;所有合格的成品,由FQC在标识上盖合格章后通知其工序打包,并由FQC开“进仓单”并作好成品标识及贴上“产品合格证”。仓管人员按“进仓单”放置在指定区域内。品管人员将整个生产过程的检验记录作好保存。
5.3.4 当仓库在出货时,仓管员会通知FQC作一般性重检,以防止成品因受潮损坏。合格则填写“FQC出货检验合格报告”,一式两联:一联交仓管员装车出货,一联交文员保管。
6.参考文件:
6.1《不合格品控制程序》
6.2《纠正与预防措施》
7.记录: 保存地点 保存时间 附件序号
7.1 MIL-105E(来料与成品)抽检标准(FM-QA-10/A0)品管部 永久 附件一
7.2 进料验收单(FM-QA-01/A0) 品管部 半年 附件二
7.3 IQC不合格报告(FM-QA-11/A0) 品管部 半年 附件三
7.4 PQC检验日报表(FM-QA-12/A0) 品管部 半年 附件四
7.5 PQC不合格报告(FM-QA-13/A0) 品管部 半年 附件五
7.6 FQC不合格报告(FM-QA-05/A0) 品管部 半年 附件六
7.7 制程巡检记录表(纸箱)(FM-QA-06/A0)品管部 一个月 附件七
7.8 制程巡检记录表(彩印)(FM-QA-07/A0)品管部 一个月 附件八
7.9 不良品传票 (FM-QA-08/A0) 品管部 无需 附件九
7.10 PQC日检验标准单(FM-QA-23/A0)品管部 一年 附件十
7.11 产品标识单(仓库)(FM-SD-07/A0) 仓库 无需 附件十一
7.12 产品标识单(品管)(FM-QA-09/A0) 品管部 无需 附件十二
7.13 成品标识单(FM-QA-03/A0) 品管部 无需 附件十三
7.14 进仓单(FM-SD-12/A0) 品管部 一个月 附件十四
7.15 产品合格证(FM-QA-18/A0) 品管部 无需 附件十五
FQC出货检验合格报告(FM-QA-26/A0)品管/仓库 一个月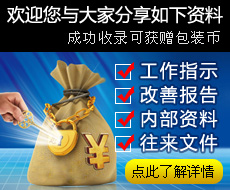