瓦楞纸箱客户质量投诉焦点
瓦楞纸箱的客户质量投诉焦点
一、瓦楞纸板的质量控制
项目1:瓦楞纸板成型
质量标准:瓦楞纸板无倒瓦现象,瓦楞无压破、挤坏缺陷。
检验方法:用美工刀切开,目测切口进行确认。
实例:在瓦楞纸板生产过程中,有时由于纵切刀具不够锋利,瓦楞纸板边缘会出现压扁现象,在外观检验时容易引起顾客的误解,认定为纸板倒瓦,当然也包括有些恶意消费的顾客把这种现象说成是倒瓦已达到退货或折扣的目的。遇到这种质量投诉时,可以将瓦楞纸板从中间切开,与合格的瓦楞纸板进行比对来说服顾客,但为满足顾客,在生产的过程要特别注意控制好纸板边缘不能出现压扁的现象。
项目2:瓦楞纸板厚度
质量标准:C>3.5mm,B>2.5mm ,E>1.1mm BC>6mm ,BE>3.6mm.
检验方法:采用瓦楞纸板厚度测定仪来检测瓦楞纸板厚度,应测定瓦楞纸板的两侧以及中央三处,以最低部分不能小于以上尺寸为原则。对于个别客户有特殊厚度要求的尤其要加强控制。为了便于以后对产品的质量追溯,每份产品都要保留一份瓦楞纸板项目的检验表,由于留取每份纸板的样品不便于管理,可以将瓦楞纸板横向切开,象盖图章一样将瓦楞纸板的楞型盖到检验表上。
项目3:翘曲度
质量标准:虽然国家标准中规定了瓦楞纸板翘曲的范围,为加强质量控制,建议应以要求纸板无翘曲为原则。
检验方法:将瓦楞纸板放到一个平面上进行目测以及尺寸测量。
特例:由于决定瓦楞纸板平整度的因素较多,时常会发生瓦楞纸板出现翘曲的现象。因为瓦楞纸板刚生产完以后还带有一定的热度,在此时采取措施进行纸板平整度的校正很有效果,通常将刚生产完的纸板每15张左右正反叠放,然后上面用重物压住来进行校正。这里重点谈谈单面瓦的生产控制,因为单面瓦在生产的过程中是单面施胶,在干燥过程中,因为纸张的收缩极易造成翘曲现象,后通过降低干燥过程中蒸汽压力的方法取得了比较明显的效果,生产出来的瓦楞纸板平整度较好。另外,在胶印贴面的过程中,瓦楞纸板也极易出现翘曲现象,在这里我们也等同于瓦楞纸板翘曲一并进行讨论。在一个阶段,我们曾认为这种弯曲不可避免没有认真去对待,后来顾客连续投诉,我们用国家标准中要求的瓦楞纸板翘曲标准来向顾客解释,顾客就根本不接受,尤其是需要在自动包装机上自动包装产品,一张瓦楞纸板的翘曲有时会造成整个生产线的堵塞,影响到顾客的生产效率。后来进行了加装水辊等措施,效果不是很明显,有时因为加水太多反而使瓦楞纸板水分加大影响了纸板的强度。最后在管理环节加大了力度,对刚贴完面的瓦楞纸板也象主机刚生产的纸板一样每10张左右进行叠放施压,效果较好。有些长期库存的瓦楞纸箱原来因为翘曲而报废,经试验,在里纸上人工摸水后正反叠放捆扎施压而得到了解决翘曲问题。
项目4:瓦楞纸板加工尺寸偏差
质量标准:瓦楞纸板尺寸偏差要求宽度±1mm,长度±2mm。
检验方法:用量尺测量。对于一出几个的瓦楞纸板可采取简单快速的方法进行测量:同时平行将纸板样品取出,用量尺测量一张纸板的尺寸,将其他几张纸板调转180度以后与该张纸板进行比较看纸板的对齐情况来判定。
项目5:瓦楞纸板粘合强度
质量标准:瓦楞纸板完全粘合,特别是要注意纸边脱胶或假粘合现象。
检验方法:将瓦楞纸板实际撕开检验、用手指按压、目测等方法。要强调的是,为了防止假粘合造成整批纸板的报废,纸板的首件检验一定要整张纸板来撕开进行检验。
项目6: 瓦楞纸板的杠线情况
质量标准:瓦楞纸板无断杠现象,折叠时能按直线折叠。
检验方法:用手将瓦楞纸板的杠线折弯确认。PET杠线因为较浅,顾客有时在使用的过程中由于摇盖不能正常折叠影响使用而退货,不得不用人工再折摇盖来进行校正,浪费了很多人力,因此对于PET杠线要加强检验。
项目7:瓦楞纸板的纸边及刀口情况
质量标准:瓦楞纸板无纸边不齐、无纸屑、无挤压、破损等缺陷。
检验方法:目测确认。需要说明的一点是,对于食品瓦楞纸箱,尤其是出口食品瓦楞纸箱,纸屑如果掉入包装箱内将按照异物来处理,所以对于刀口及切边不齐的检验要引起足够的重视。
项目8:瓦楞纸板的用纸控制。
质量标准:严格按照顾客要求的用纸进行生产。
在瓦楞纸板的生产过程中经常会碰到某份产品的订单量小,该份产品与上一份产品用纸类似的情况,有时在生产的过程中就给把订单量小的采用上一份的用纸一并给生产出来,这样替代用纸都是超过顾客的规定用纸标准,不能保证用纸的稳定性,一旦顾客认可了替代用纸的产品,而再按照顾客的实际用纸生产的产品,二者比较起来质量就会有差异,顾客就会产生疑义而投诉。因此要严格按照顾客要求的用纸进行生产,发生替代用纸时一定要提前与顾客进行沟通。
项目9:水分的控制
质量标准:瓦楞纸板的水分的控制在10±2%。
生产纸板所用原纸的含水率、预热烘干、原纸原料和粘合剂的特性、纸板粘合后进行烘干和冷却工艺以及生产和流通环境都会影响到瓦楞纸板含水率。
瓦楞纸板水分控制的主要方法有以下几种:
对于入厂的原纸的含水量要严格地控制。按国家标准的规定,原纸的交货状态的含水量一般为9%~12%。首先,在原纸的采购中,要把好质量关,对进厂的原纸含水量进行严格的检验,要求供应商供应合格的原纸。
另外,原纸储存一定要设立单独的库房,温度一般在15~20℃,相对湿度一般在30%~40%。不要放在露天里,这样容易造成原纸含水量的变化,而且造成两端及中部的含水量不一致。
进行合理的温度控制。温度是影响瓦楞纸板质量的决定因素之一。在瓦楞纸板生产过程中要进行合理的温度控制。温度的高低既能调整原纸的含水量,又能影响原纸的温度,使粘合剂在合理的时间内固化。
在瓦楞纸板生产线上设置有许多预热器和烘干板,用来调节原纸和单面纸板的含水量,并使粘合剂固化,粘合好各层瓦楞纸板。
对粘合剂的质量、上胶量的大小、含水量的大小、稀稠等进行合理的调控。
如果粘合剂含水量大,粘合剂稀、渗透快,纸板的含水量就高,反之含水量就小。当上胶量大时,纸板的含水量就大;上胶量少,含水量就少。所以要严格按照粘合剂的含水量和配比以及搅拌时间进行制胶,掌握好粘合剂的粘度。
二、瓦楞纸箱印刷质量问题面面观
瓦楞纸箱的印刷品质,直接决定着顾客对产品的第一印象。对印刷外观质量,顾客是越来越挑剔,极容易发现问题,产生抱怨,甚至引发投诉。常见的瓦楞纸箱印刷质量问题主要包括以下几个方面,只要在瓦楞纸箱的印刷过程中做到有效预防,避免类似印刷质量问题的发生,就会赢得顾客对印刷品质的认可。
瓦楞纸箱尺寸不准确
该问题主要是由于瓦楞纸板长度和宽度方向的分切压线位置不准确引起的。一方面是对印刷开槽刀和纸板压线轮进行调整时发生位置错误;另一方面是由于在批量生产过程中,开槽刀和纸板压线轮发生松动,位置产生偏移金属包装,需要对开槽刀和纸板压线轮的紧固装置进行检修,以确保紧固件的正常运行,使设备稳定工作。
印刷版面位置不准确
这里主要指整体印刷版面的不同印刷版之间的相对距离出现偏差,导致版面中部分印刷版位置不准或影响到整体印刷版面的协调。主要是因为排版位置不准确导致。另外,如果出现版面位置整体偏移检测系统及仪器,也可能是由于在印刷时挂版位置偏移或模切、开槽分切位置调整不准所致。
印刷版材引起的印刷质量差
主要表现在印刷表面有刮伤痕迹、字迹不清晰或字体图象变形等情况。
印刷版材的厚度要保持一致性,其公差一般要求在±0.05mm之间,印版的高低差会造成吃墨不均匀,严重影响印刷质量和效率,因此,在印刷版材入厂检验时应严格控制。同时,印刷版材使用时间长后会出现磨损或老化现象,应及时更换,以免影响到印刷效果。
网点印刷堵塞
在网点版印刷时容易出现网点堵塞现象,主要是由于印刷版的网点线数与印刷辊网线数不匹配导致。另外,网点和细字最好采用弹性低、变形恢复慢的印版较能保持印版尖锐边缘的表现。网点版印刷对油墨质量要求也较高,需要使用较高档水性油墨,方可获得良好的印刷效果。在印刷时印刷压力调整过大,水性油墨上墨量大、印刷版上有污垢或印刷版材厚度不均匀都会造成印刷模糊。
印刷字迹或图像变形
主要原因是由于在进行印刷版制作时,没有考虑到平面变弧形时的印刷版延伸率或换算的延伸率与实际产生的延伸率不一致,这里最明显的是在印刷精确的圆圈时要特别注意,另外,印刷压力过大或制作的印刷版不标准都容易造成印刷字迹及图象产生变形。
套印不准
套印不准现象比较普遍,企业往往将套印不准的问题归结于印刷机的精度不够,这具有片面性。实际上影响印刷套印的因素很多加网,主要包括瓦楞纸板翘曲、印刷套色版叠印部分的设计不合理、套印版的排版准确度以及印刷时油墨颜色的排列顺序,只有综合考虑,全面调整到位,才能保证印刷套色准确
瓦楞纸板压溃
印刷时,由于印版向瓦楞纸板施压过大,导致瓦楞纸板压溃、变薄,主要是由于印刷版压过大。另外乐凯二胶,印版的衬垫厚度不一致、印刷磨损程度不一致或印版滚筒贴胶带导致厚度不均匀,都会引发不同程度的印刷质量问题。
印迹上有小孔或鱼眼状孔
印刷版面上频繁出现没有油墨的空白点,主要是由于油墨起泡或为解决起泡现象添加过量的消泡剂、印刷版上有小孔、纸板面纸表面粗糙引起。
印刷颜色不一致或覆盖不均匀
顾客对瓦楞纸箱的印刷颜色要求一般都比较挑剔,这直接影响到瓦楞纸箱的外观质量,主要表现在不同批次之间或同一批次之间油墨印刷颜色不一致,出现或深或浅现象,以及油墨颜色覆盖不均匀,存在的露底现象。
油墨颜色不一致是指与顾客提供的标准颜色相比较,所印刷出来的颜色存在饱和度和亮度不一现象,并且不同批次之间或同一批次之间存在颜色偏差。主要原因是由于供货的油墨颜色存在偏差、生产过程中对水性油墨用水冲淡量大、油墨在使用过程中粘度发生变化、墨辊换色印刷时上墨系统清洗不净等造成的。最好的办法是在印刷第一批次产品时,将顾客确认的印刷样采集存档,以便在以后印刷同一产品时进行核对比较。
水性印刷最适用的油墨粘度在17~25秒之间,对印刷颜色要求严格的,油墨粘度要稳定在一定的范围内。
油墨覆盖不均匀是指油墨在印刷版上着墨不均匀,出现印刷露底现象。瓦楞纸箱的面纸质量粗糙、油墨粘度低、印刷版表面有污垢或印刷版硬度大、厚度不均匀、印刷时压力调整不到位、油墨干燥快、印刷机着墨辊网孔堵塞等都容易引起油墨覆盖不均匀。
印刷字迹模糊、油墨溢出字迹轮廓外、印迹周围有晕圈
该现象主要是由于油墨本身的产品质量影响(如油墨粘度大或上胶量大、油墨干燥快等)、印刷滚筒高速运转时油墨喷溅、纸板表面有纸屑或灰尘、印刷压力调整过大、印刷版挂版松动、印刷版不水平、磨损、弯曲、表面有污垢或树脂版与橡胶版组合使用、印刷版清底过浅导致。
油墨的干燥速度快慢会影响印刷速度,一般要求在高速印刷时,油墨干燥速度快为理想,但干燥速度过快会使印版表面形成一层薄膜,影响油墨的转印,造成印版间隙形成积墨、结块而使印刷字迹模糊,而且油墨不易保存,容易凝固变质。在印刷时不同颜色的油墨按先后顺序粘度应递减,先涂上的颜色油墨干燥要比后涂上的颜色干燥速度快。
三、其他质量投诉
瓦楞纸板发软,手感差,直接给客户造成瓦楞纸板物理强度指标低的印象。
原材料强度指标低,是导致纸板发软的主要原因。瓦楞原纸的质量的好坏直接影响瓦楞纸箱的抗压强度,选择高强度瓦楞原纸,可以制造出坚挺而富有弹性的瓦楞纸箱。另外,纸板倒瓦也会导致纸板发软,应重点在生产线工序和印刷工序印刷压力调整上下工夫。
瓦楞箱纸板发软,原材料的含水率和施胶量过大是重要原因。由于施胶量过大,胶液中的水分渗透到瓦楞中致使瓦楞变软,进入烘干板后,纸板水分得不到充分散发使纸板发软。
瓦楞纸板横向压痕过浅 ,出现摇盖折叠走单线或折叠时横向压痕线不直;瓦楞纸板纵向压痕过深,出现里纸破裂现象。
瓦楞纸板压痕是瓦楞纸板成箱加工的必要工序之一,压痕质量的好坏对瓦楞纸板在钉箱折叠或成箱使用中起着重要的作用,压痕的深浅和位置准确度不同,往往会导致瓦楞纸箱尺寸发生偏差。
瓦楞纸板横向压痕一般在瓦楞纸板生产线实现,采用双凸缘压痕,纵向压痕一般在印刷开槽机上完成,采用单凸缘压痕。一般单凸缘压痕宽度在6-12mm,双凸缘压痕宽度在10-16mm左右。
压痕的原则是通过调整压痕的压力,以达到易折、压痕明显、面里纸不破裂为标准。
对横向压痕,上下轮的中心位置要对齐,并且压痕要压透,即压得没有空隙,一般要求五层瓦楞纸板压痕处的厚度为2mm左右。对纵向压痕,痕的上下轮间隙不宜调整过小,同时要求瓦楞纸板含水率不宜过低,以防加工时造成瓦楞纸板破裂。
瓦楞纸箱摇盖断裂
摇盖耐折度是瓦楞纸板质量的重要指标之一。根据国家标准GB6543-86规定:瓦楞纸箱摇盖经开、合180度往复5次以上,1、2类箱面层和里层都不得有裂缝,3类箱板外面层不得有裂缝,内里层裂缝长度总和不得大于70mm。但在使用中,客户要求严格得多,他们要求摇盖向外里下折180度,里外面纸都不得有裂缝,保证生产过程中满足现场使用要求。这需要控制好原材料的质量,尽量避免使用纸浆粗糙的低档瓦楞原纸,这样的瓦楞原纸可能会在摇盖折叠时将面纸顶破。
纸和瓦楞纸板太干也是造成摇盖折线断裂的重要原因,在生产过程中,一定要控制好纸和瓦楞纸板的含水率。
摇盖折线的压痕一定要控制好,使压痕适中,如果生产中发现摇盖断裂在瓦楞纸板离机后立即对里面纸摇盖处进行喷雾,并将摇盖向两边折到底一二次,可大大提高摇盖的耐折度。
版面印刷错误
瓦楞纸箱的版面多采用文字印刷,极容易发生错误,一旦设计版面出现问题又未曾得到纠正,后果将不堪设想。一般情况下,往往瓦楞纸箱的版面错误非常容易让人疏忽,经常是多一字,或小一字,错一字,校对时必须一一进行校对勘误,严格把关,否则会因小小的错误导致整批瓦楞纸箱报废。企业对瓦楞纸箱版面的校对工作必须重视起来,绝不可以放松。
印刷颜色不统一或瓦楞纸箱面纸颜色不统一
印刷色样在不同批次供货中产生差异,或不符合客户要求的色样,这种情况,一般将会被退货。这要求在严格控制油墨色相稳定的同时,最好的办法是在印刷第一批次产品时,将印刷色样存档,以使在以后印刷同一产品时进行核对,做到印刷颜色统一。
由于瓦楞纸箱的面纸生产厂家不同,面纸颜色也存在差异,即使同一厂家的箱板纸,不同批次也存在色差。这要求在原材料进厂检验时严格控制,对纸样存档,最起码要对同一厂家的箱板纸进行统一,在生产时,相同的瓦楞纸箱采用同一家箱板纸,保持面纸颜色统一。
瓦楞纸箱尺寸不准确
瓦楞纸箱的设计制造离不开尺寸,尺寸搞错了,制造出的瓦楞纸箱也就成了废品。瓦楞纸箱的尺寸分为内径尺寸、外径尺寸、加工尺寸,客户一般都对瓦楞纸箱的内尺寸要求严格。瓦楞纸箱的内径尺寸必须保证内装物能够装得下,一般等于内装物的最大外径尺寸加上参数3~7mm 。外径尺寸是在流通中使用的尺寸,对出口瓦楞纸箱来说,外径尺寸要求十分严格,否则会因尺寸影响集装箱装运。这要求在生产过程中严格控制好生产线纸板尺寸、印刷开槽压线尺寸的同时,抓好钉箱和粘箱工序尺寸控制。
瓦楞纸箱面纸有折痕
瓦楞纸箱面纸有折痕主要是储存和运输过程中造成的,这一流通环节,往往都引不起企业的重视,缺乏质量监控力度。另外在瓦楞纸箱生产过程中,面纸的强度不够,压力辊中高度不够以及面纸的含水率不均匀也会造成面纸带上折。
瓦楞纸箱表面曲翘将导致在堆码时出现瓦楞纸箱折的现象,导致瓦楞纸箱的承重能力下降,同时应保证瓦楞纸箱在尽量短的时间内使用,避免长期存放导致自然风干而造成的表面翘曲现象的出现。
瓦楞纸箱表面透楞,不平整。
瓦楞纸箱表面透楞,影响到瓦楞纸箱整体视觉美观,且手感不平滑,不能满足外观精细化的要求。主要是由于面纸选用不好,克重低造成,其次是在瓦楞纸板生产过程中,面纸湿度控制不当造成。
瓦楞纸箱箱盖切口处撕裂或封箱后折角存在空洞
主要表现在瓦楞纸箱成箱时出现箱盖切口超过箱盖折叠压痕线或封箱后折角存在空洞的现象,导致此处应力增大,易使瓦楞纸箱此处出现撕裂现象。在检验过程中严格控制瓦楞纸箱切口顶端处于折叠压痕线的中间位置,且保证切口与箱体的折叠压痕成直线。
瓦楞纸箱的装订质量不符合要求
瓦楞纸箱的装订质量包括箱钉间距和装订后底面的平整度。装订后底面不平整将直接影响到包装箱的承力的均匀性。
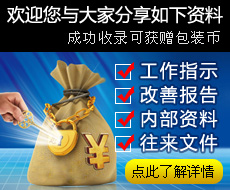