纸包装印刷企业质量过程控制管理点滴
纸包装印刷企业质量过程控制管理点滴
从实施ISO质量管理体系的角度看,基本状况可描述如下:
已有相当部分纸包装印刷企业已建立了IS09001质量管理体系,但从实质上看,能够深刻理解IS09001质量管理体系的内涵,并能够有效实施的企业只有其中的一部分。
相比较而言,欧美企业比较重视体系管理,希望以系统性的管理来约束和规范操作人员,达到对生产过程的掌控;日本企业特别强调从业人员的责任心和敬业精神,籍此通过较高的个人工作质量来达到对生产过程的稳定控制。目前,我国印刷企业走欧美体系管理模式的居多,对日本企业的管理模式了解相对较少。
初看日本纸包装印刷企业的质量管理,有种"个体户"式的感觉。一家具有代表性的日本纸包装印刷企业--森·纸业,全公司近150人,年产值约4.0亿人民币,但没有设立专门的品质管理部门。全公司只有3个人负责质量管理,2人专职负责进货检验。该公司的印刷品以日用品包装为主,品种繁多,有纸板盒,也有瓦楞盒。其生产工序有:印前、印刷、烫金、压光、贴窗、裱瓦楞、模切和糊盒。从技术装备看,其先进性并不是顶尖级,只能算"二流"水准,但其质量控制水平可谓世界一流。经过与该公司的生产厂长深入交流,以及在车间实际所看到的情况,给我们的印象是:日本企业重视本工序的责任控制。这种责任控制还不仅局限于质量,也体现在生产效益和环境5S上。
在印刷车间,通常是两台印刷机配置5个人。印刷过程中发现质量问题时,机长首先用插条的方式将有问题的印品进行标识,并将该栈板的印品暂放在旁边。待其可以翻动时,机台人员抽空(机器仍在正常生产)单独对其进行整理,将其中的不良品挑出来,做好标识,随正式产品流转到下一工序。印刷之后没有所谓的"拣大张"的印品整理组。后道各工序也是如此,所有工序所发生的问题全由本工序负责。在糊盒工序,我们看到一台糊盒机配三个人。他们分别是机长1人(负责操作机器、抽查糊盒质量和辅助装箱)、加料一人和收料一人。在糊盒机车速为60000个/小时(面巾盒)的情况下,他们还要负责装箱、封箱、贴标签和码放栈板。若不是亲眼所见,你是不相信的。另外,工序间不需要重复装纸。上道工序收料时,就已将纸堆理齐,下道工序可直接将整栈板推上机器开始作业。这也是本工序落实责任控制的结果。整个生产流程中没有专职巡检员"帮助"操作者多把一道质量关。该公司甚至没有出厂前的最终检验。日本人对包装质量的挑剔在世界上是独一无二的。
与欧美包装印刷企业相比,我们的纸包装印刷企业的系统性质量管理尚有较大差距,与日本企业相比,我们从业人员的敬业精神和责任心尚有更大的差距。作为国内包装印刷企业,要承接欧美品牌客户的订单,必须注意系统的质量管理体系的建设与有效实施,而要承接日本的品牌客户订单,必须求真、务实,步步落到实处。鉴于中国的包装印刷企业既不同于欧美企业,又有别于日本企业,为此,我们中国印刷企业应汲取各家之所长,把两大流派的管理模式有机结合起来。
1. 设立一个权威性的品质控制部门,人员不要太多,但素质要高。该部门应独立于生产,以此推动公司质量体系的持续改善。这种改善应该是强制性的、权威性的。只有这样,才能在全公司逐渐形成一种重视品质的氛围。这一点要成功,其前提条件是企业的第一领导人必须要有这种意识。
2. 以培训为主,奖惩结合的方式,提高各工序操作者的质量意识。观念这种东西不是一天、两天、一个月、两个月就能改变的。对于责任心欠佳的操作人员更是如此。由于缺乏责任心,他们对自己的过失造成的产品质量损失不具有内疚感。在日本、香港和新加坡,纸包装印刷企业其实很少有名目繁多的质量考核,效率考核条例,但他们照样有好的品质和高的生产效率。这大概与从业人员的受教育背景、责任心和职业道德等意识有关。因此说,针对国内包装印刷业工人的现状,培训是十分重要的。只有通过持续培训,才能对这支队伍进行潜移默化的影响,同时辅以激励和处罚措施,逐步培育员工的责任意识感。
3. 系统地、务实地开展质量改善活动。如建立月质量分析会,对一个月以来所发现的质量问题,运用统计分析工具作汇总分析,并根据二八法则找出需要改善的主要质量问题,制定改善措施,明确责任人及完成日期,会后由品质管理部门进行跟催和关闭;对于典型的质量案例,品质管理部门应迅速组织召开现场质量专题会,对相关人员作现场教育,并分析真因、制定措施,形成会议纪要,会后由品质管理部门进行跟催和关闭;对于复杂的质量问题,还必须成立特别的质量改善小组(QIT),按项目管理的方法予以实施。只有这样双管齐下,才能在全公司形成以质量目标为导向的观念。当我们切实走完IS0质量管理的历程之后,就会向日本企业那样,品质管理部门也就失去了它存在的意义。
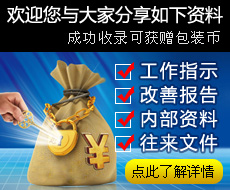