制程及最终品质检验实验控制程序
制程及最终检验和实验控制程序
1.0目的:
保证所有产品在生产过程中都通过规定的检验后才进入下道工序或入仓
2.0适用范围﹕
本程序适用于公司内所有正在生产的半成品﹑成品。
3.0职责
3.1 生产作业员负责自检工作﹐并同品管人员一道做好首件检查。
3.2 PQC负责巡回检查﹐质量控制点的检查﹐半成品的检验。
3.3 OQC负责成品的检验。
4.0定义
PQC﹕制程质量检验人员。
OQC﹕成品质量检验人员。
5.0作业程序
5.1 过程检验
5.1.1首件检查
l 在规定要进行首件检查的工序﹐每班次开始或生产过程中因换人﹑换料﹑换品种以及换工装﹑设备调整等改变工序条件后生产的1~3件产品﹐操作者自检后﹐还必须送PQC做首件检查﹐首件检查结果记录于“半成品检验报告”首件检查记录栏中。
l 首件检查合格时﹐由PQC在首件上和生产单上签名确认﹐通知操作者继续作业﹐首件检查不合格时﹐PQC向操作者指出不合格部位﹐要求其改进﹐操作者返工或重新加工首件﹐直至检验合格﹐方可继续生产。
5.1.2自主检查
生产车间作业员要在生产中进行自主检验﹐自主检查中作业员如发现产品质量异常时﹐应及时停止作业﹐并向组长报告﹐寻求改善对策,并将结果记录在生产日报上。
5.1.3巡回检验
PQC应不定时地对各工序(或机台)进行巡查﹐作好“半成品检验报告”﹐巡查时如发现问题及时指导作业者或联系有关人员加以纠正﹐巡查中发现的不合格品应做好标记并适当隔离。
5.1.4质量控制点的检查。
5.1.4.1根据本公司的生产工艺特点﹐设置双面机﹑水墨印刷﹑彩印﹑啤机四个主要工序控制点。相关PQC人员对上述四个控制点实行首检﹐抽检﹑末检工作。
5.1.4.2双面机纸板的控制。
PQC人员根据“纸板外观检验标准”进行检验﹐并将检验结果记录在“纸板检验报告”上﹐发现问题及时要求机手改善。
5.1.4.3水墨印刷的控制。
PQC人员根据生产单﹑唛头单﹑样办对水墨印刷品进行首件检验及首件综合判定﹐检验合格在生产单﹑唛头单上签名确认方可批量生产﹐并不定时进行抽检﹐发现问题及时反馈改善﹐每批完成时均应进行末件检验﹐确保批量一致性﹐末件如不合格则整批货全检﹐所有的检验结果记录于“(印刷)半成品检验报告上”。
5.1.4.4彩印的控制。
PQC人员根据生产单﹑样办﹑色稿对彩印品进行首件检验及首件综合判定﹐检验合格后可批量生产﹐在彩印过程中不定时进行抽检﹐发现不良要求机手改善﹐批量完成作末件检查﹐确保批量的一致性﹐末件如不合格则整批货全检。所有检验结果填在检验报告上。
5.1.4.5啤机的控制。
PQC人员根据生产单﹑样办﹑对啤出货品进行首检﹐检验合格后在首件﹐生产单上签名确认﹐留好首件方可批量生产﹐不定时抽查生产过程的货品﹐发现问题要求机手及时改善﹐货品做完做末件检查﹐确保批量一致﹐末件如不合格则整批货全检。将所有检验结果记录于“(啤机)半成品报告上”。
5.2 成品检查。
5.2.1成品检查前﹐应确定所规定的进料检查﹑过程检查已经完成﹐且检验结果合格。
5.2.2OQC人员抽样检验依照“抽样计划”执行。
5.2.3OQC人员按照样办﹑生产单﹑唛头单﹐参照“成品质量检查”检验,检验内容包括材质﹑尺寸﹑印刷内容﹑裁切﹑成型结构﹑包装等。
5.2.4若客户另有标准则参考“质量标准卡”。新产品打办时的“质量标准卡”由技术部人员填写﹔生产过程中“质量标准卡”的增修由品管部人员执行。
5.2.5检验合格后﹐OQC在每板成品单上加盖“QCPASSED”印﹐填写“成品检验报告”。若检验不合格﹐则按“不合格品控制程序”执行。
6.0 相关文件
6.1 抽样计划WI-QC-024
6.2成品质量检查WI-QC-011
6.3不合格品控制程序OP25
6.4纸品外观检验标准WI-QC-025
7.0 相关表格
7.1纸板检验报告RE-OP23-01
7.2 半成品检验报告RE-OP23-02
7.3 成品检验报告RE-OP23-03
7.4 品质标准卡RE-OP15-07
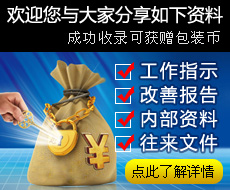